How does a wellhead work?
A wellhead is a crucial component in oil and gas drilling operations, serving as the surface termination of a wellbore. It works by providing a structural interface for the drilling and production equipment used to extract hydrocarbons from underground reservoirs. The wellhead's primary function is to maintain pressure control of a producing well, preventing the uncontrolled release of oil or gas. It accomplishes this through a series of valves, spools, and adaptors that regulate pressure, direct flow, and enable the installation of various equipment such as blowout preventers (BOPs) and production trees. By effectively managing pressure and flow, wellheads ensure safe and efficient drilling operations, protect the environment from potential spills, and facilitate the controlled extraction of valuable resources throughout the well's lifecycle.
Basics of Wellhead Systems
Components of a Wellhead
A wellhead is a critical part of an oil or gas well, designed to provide structural integrity and control during the drilling and production phases. The casing head serves as the foundational component, anchoring the surface casing to the wellhead assembly. It is the base that supports the entire well system. On top of the casing head is the tubing head, which is responsible for supporting the production tubing string that carries the produced fluids from the reservoir to the surface. To manage flow and pressure, the products are equipped with various types of valves, including the master valve, which is the main shut-off valve, and wing valves, which are used for additional control during operations. In addition, spools and adaptors are employed to provide flexibility and facilitate the proper configuration of the wellhead to meet different operational needs. Together, these components work in unison to ensure the safe and efficient operation of the well.
Types of Wellheads
Wellheads come in different types, each tailored to meet specific operational and environmental conditions. Surface wellheads are typically used in land-based drilling operations, offering a stable and accessible configuration for routine maintenance and control. In contrast, subsea wellheads are specifically designed for offshore drilling operations, built to withstand the challenges of deep-water environments, such as high pressure and corrosive conditions. For areas with limited space, compact wellheads are often employed, providing a more compact solution without compromising functionality. Additionally, multi-bowl wellheads are used when multiple casing strings are required, offering the capability to accommodate complex well designs. The selection of a wellhead type depends on several factors, including well depth, pressure requirements, environmental challenges, and the overall design of the well.
Wellhead Pressure Control
Maintaining pressure control is one of the primary functions of the product. The wellhead system utilizes a combination of mechanical and hydraulic components to regulate the pressures encountered during drilling and production activities. Pressure gauges are installed to monitor internal pressures within the well, providing real-time data that helps in maintaining safe operational conditions. Adjustable chokes, which are installed in the system, allow for precise control of the flow rate, enabling operators to adjust the flow of production fluids based on pressure levels. In critical situations, such as when there is a risk of a blowout, safety valves are activated to quickly shut off the flow of fluids, preventing accidents and minimizing the risk to personnel and equipment. These pressure control mechanisms are essential not only for maintaining the integrity of the well but also for ensuring the safety of the operation and protecting the surrounding environment.
How Wellhead Equipment Ensures Safe Drilling Operations
Blowout Prevention Systems
Wellheads are essential components in preventing blowouts, which are uncontrolled releases of oil or gas from a well. They provide a stable platform for mounting blowout preventers (BOPs), which are crucial safety devices. BOPs are designed to quickly seal the wellbore in the event of an unexpected pressure surge, preventing dangerous blowouts. The wellhead’s robust design and precise engineering ensure a secure connection between the BOP stack and the well, creating a reliable barrier that can handle extreme pressure conditions. This connection is vital for maintaining control over the well and protecting the surrounding environment and personnel.
Wellhead Integrity Testing
Maintaining the integrity of a wellhead is paramount to ensuring the safety and success of drilling and production activities. Regular integrity testing is conducted to verify that the product components can withstand the high pressures and environmental conditions they are subjected to. One of the most common tests is a pressure test, which checks the ability of seals and valves to maintain a secure and pressure-tight connection. Visual inspections are also performed to identify any visible signs of wear, corrosion, or damage. For a more detailed examination, advanced techniques such as ultrasonic testing are used to detect internal flaws in the product materials that may not be visible to the naked eye. These thorough testing procedures are crucial in ensuring the long-term reliability and safety of the product throughout its operational life.
Emergency Shutdown Systems
In critical situations, it is vital to be able to isolate the well quickly to prevent further risk. Wellheads are equipped with emergency shutdown systems that can perform this task automatically. These systems typically consist of fail-safe valves that close in response to a loss of hydraulic pressure, effectively isolating the well from the surrounding equipment and environment. The integration of remote operation capabilities allows for quick action, even in unmanned or offshore installations. The ability to remotely activate shutdown systems is particularly important in locations where immediate access may not be possible. By linking the product emergency systems to broader platform safety protocols, the overall safety of the operation is significantly enhanced, ensuring a rapid and coordinated response to any potential hazards.
Case Studies: Successful Wellhead Operations
Deepwater Wellhead Installation
A notable case study in deepwater wellhead installation took place in the Gulf of Mexico, where engineers successfully deployed a wellhead system in extreme water depths. The project faced significant challenges, primarily due to the vast depths, exceeding 10,000 feet, and the immense pressures that come with such depths. To overcome these obstacles, engineers utilized cutting-edge subsea wellhead technology, which incorporated advanced fatigue-resistant materials and state-of-the-art sealing mechanisms. These innovations ensured that the wellhead could endure the immense pressures, prevent leaks, and remain structurally sound throughout the drilling process. The design's robustness was crucial in ensuring the wellhead's ability to withstand both the mechanical stresses from the deepwater environment and the challenges posed by harsh marine conditions.
Arctic Wellhead Performance
In the harsh and unforgiving environment of the Arctic, wellhead systems face unique challenges due to extremely low temperatures and ice forces. A successful case study from Alaska's North Slope illustrates the resilience of specialized Arctic wellheads designed to thrive in such conditions. The wellheads used advanced materials that were highly resistant to low-temperature embrittlement, ensuring they could maintain their structural integrity even in temperatures as low as -40°F. Additionally, these systems were equipped with innovative heating mechanisms that prevented freezing, which could otherwise compromise their functionality. This combination of advanced materials and technology allowed the wellheads to perform reliably, ensuring continuous, safe production in one of the most challenging drilling environments on Earth. These systems demonstrated the importance of designing wellheads tailored to extreme climates, enabling resource extraction in areas where other technologies might fail.
High-Pressure, High-Temperature Wellhead Application
A compelling case study from the Middle East highlights the successful deployment of wellheads in high-pressure, high-temperature (HPHT) conditions. The wellhead system was designed to withstand pressures up to 15,000 psi and temperatures exceeding 350°F. Advanced metallurgy and sealing technologies were employed to ensure long-term integrity. The wellhead's performance in these extreme conditions enabled the safe extraction of valuable resources from previously inaccessible reservoirs, showcasing the critical role of wellhead technology in expanding the frontiers of oil and gas exploration.
Source: Oil & Gas field Quality control
FAQ about Wellhead
What is the primary function of a wellhead?
The primary function of a wellhead is to provide pressure control and a structural interface for drilling and production equipment. It serves as a critical safety barrier, preventing the uncontrolled release of oil or gas from the well.
How long does a typical wellhead last?
The lifespan of a wellhead can vary depending on factors such as operating conditions, maintenance practices, and environmental factors. With proper care and maintenance, a wellhead can last for several decades, often matching the productive life of the well itself.
Can wellheads be used for both oil and gas wells?
Yes, wellheads are designed for use in both oil and gas wells. While there may be some differences in specific components or configurations based on the type of hydrocarbon being extracted, the fundamental principles of pressure control and equipment interface remain the same.
Understanding the intricate workings of wellheads is crucial for professionals in the oil and gas industry. These vital components ensure safe and efficient drilling operations while protecting the environment and valuable resources. For more information on wellheads and other oilfield products, please contact us at oiltools15@welongpost.com. Welong, your trusted partner in oilfield equipment solutions, is committed to providing high-quality products and expert support for all your wellhead needs.
References
1. "Fundamentals of Oil & Gas Industry Processes" by Samir K. K. (2017).
2. "Well Engineering and Construction" by M. J. Economides, K. G. Nolte (2000).
3. "Drilling Engineering: A Complete Well Planning Handbook" by Neal Adams (2012).
4. "Petroleum Engineering Handbook" by Larry W. Lake (2006).
5. "Oil & Gas Production Handbook: An Introduction to Oil and Gas Production" by V. D. Chikuni (2012).
6. "Introduction to Petroleum Engineering" by John R. Fanchi (2016).
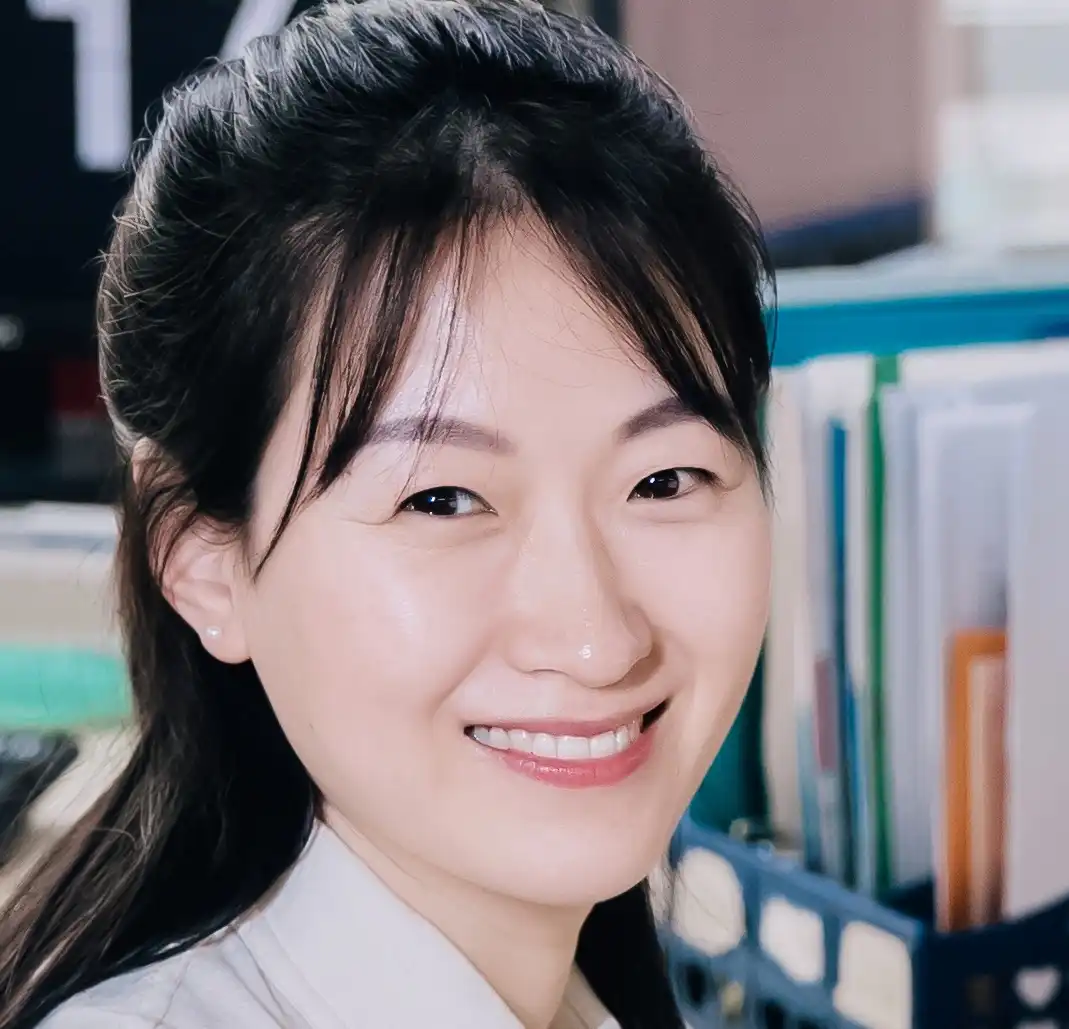
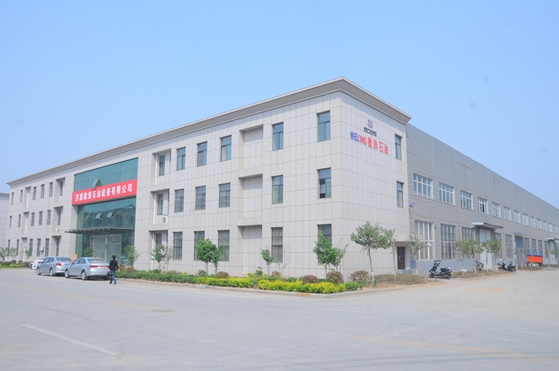
CHINA WELONG - 20+ years manufactuer in oilfield tools