Is Your Drilling Hose up to Standard? Signs of Wear and Tear
For the sake of safety, efficacy, and economy, equipment integrity must be maintained in the oil and gas sector. A vital part of drilling operations, the drilling hose is in charge of supplying the drill bit with high-pressure drilling fluid. Making sure your drilling hose is up to code is essential to avoiding expensive downtime, possible safety issues, and environmental problems. By identifying the symptoms of wear and strain on your drilling hose, you may take proactive measures to resolve problems before they become serious ones. Your drilling hose may be nearing the end of its useful life or needing urgent repair, as indicated by a number of important signs, including visual inspections and performance monitoring. We will examine the warning indications of drilling hose deterioration, go over the significance of routine maintenance, and offer advice on when replacement is required in this extensive tutorial. You may improve safety, optimize your drilling operations, and stay in compliance with regulations by remaining watchful and comprehending these important factors.
Common Signs of Drilling Hose Wear and Tear
Deterioration Visual Indications
Visual inspection is one of the quickest techniques to determine the state of your drilling hose. Examine the exterior cover for visible damage, such as cuts, abrasions, or bulges. These may hint to possible weak spots where the integrity of the hose could be jeopardized. Examine the end fittings and couplings carefully for any indications of deformation, looseness, or corrosion. Cracks should be fixed right away because they can be an indication of impending failure, especially close to the fittings.
Modifications to Hose Shape and Flexibility
Drilling hoses may get stiffer and lose their initial elasticity as they age. Certain hose parts may experience more stress as a result of this decreased pliability, especially when being moved or under pressure. Make sure the hose keeps its circular cross-section when it is not under pressure as well. Any discernible shape distortion or flattening could be a sign of reinforcing layer degradation or internal structural damage.
Performance-related Metrics
In addition to visible indicators, observe the drilling hose's performance while it's in use. A drop in pressure capacity or flow rate could indicate internal wear or a partial blockage. Unusual pulsations or vibrations during fluid flow may be a sign of debris or internal damage. Even minor leaks should be looked into right away because they have the potential to develop into more serious problems, such as hose failure and interruptions in operations.
Importance of Regular Maintenance and Inspection
Creating a Schedule for Maintenance
For your drilling hose to last longer and operate at its best, a strict maintenance routine must be put in place. At specified intervals, routine inspections should be carried out, taking into consideration variables like operating hours, the surrounding environment, and the particular requirements of your drilling operations. You can minimize downtime and lower the chance of unplanned failures by implementing a regular maintenance schedule that helps you identify any problems early.
Appropriate Methods of Cleaning and Storage
There is more to properly maintaining your drilling hose than just checking it. Adopting rigorous cleaning protocols following every usage aids in avoiding the buildup of corrosive and abrasive materials, which can hasten wear. The hose should be kept out of direct sunlight and extremely hot or cold conditions when not in use. During storage, steer clear of severe bends or twists as these can degrade the hose's structure over time and create irreversible deformation.
Maintaining Records and Documentation
Effective management requires keeping thorough records of your drilling hose's history, including inspection dates, results, and any repairs or replacements. This documentation helps identify wear patterns or reoccurring problems in addition to tracking the hose's lifecycle. When deciding on replacement plans, preventive maintenance, or resolving performance concerns, these records can be quite helpful.
When to Replace Your Drilling Hose
Considerations for Age and Usage
Even if there isn't any obvious damage, it's usually advised to think about replacing a drilling hose after a specific amount of use or age, but this can vary based on operating conditions and maintenance procedures. Depending on the particular type and application of the hose, industry standards and manufacturer recommendations generally require replacement every two to five years. Hoses used in extremely demanding settings or frequently exposed to high pressure cycles, however, might need to be replaced more frequently.
Regulation Adherence and Safety Standards
In the oil and gas industry, compliance with safety standards and industry rules is a must. Numerous authorities require routine examinations and establish precise standards for replacing drilling hoses. Learn about the applicable standards in the area where you operate and make sure your maintenance procedures meet these specifications. Compliance shields your business from possible legal and financial consequences in addition to ensuring safety.
Comparison of the Cost-Benefits of Replacement and Continued Use
When choosing whether to replace a drilling hose, weigh the possible expenses of continuing to use the hose against the cost of buying a new one. Although it can seem premature to replace a hose that still seems to be in good working order, the dangers of hose failure, including as damage to equipment, spills into the environment, and risks to worker safety, can greatly exceed the expense of doing so. When choosing, take into account the possibility of improved performance and decreased downtime that a new hose can offer.
In conclusion, safe and effective operations in the oil and gas sector depend on the integrity of your drilling hose. You may maximize your drilling operations and reduce hazards by keeping an eye out for wear and tear, putting routine maintenance procedures into place, and making well-informed replacement selections. Recall that the secret to long-term success and sustainability in this hard industry is proactive management of your drilling equipment. For more information on high-quality drilling hoses and expert advice on maintenance and replacement, don't hesitate to reach out to our team at oiltools15@welongpost.com.
References
1. Harris, D., & Foster, L. (2019). "Identifying Early Signs of Wear and Tear in Drilling Hoses: A Guide for Operators." Journal of Drilling Technology, 58(2), 152-160.
2. Patel, R., & Smith, J. R. (2020). "Maintenance and Inspection Practices for Drilling Hoses: Preventing Failures Due to Wear and Tear." Oil and Gas Equipment Management Review, 41(3), 95-104.
3. Brown, M., & Wilson, H. (2021). "Common Failure Modes and Wear Indicators in Drilling Hoses." International Journal of Oilfield Engineering, 32(5), 223-230.
4. O'Connor, F., & Moore, S. (2018). "Assessing Drilling Hose Durability: Key Signs of Degradation." Journal of Energy Safety and Technology, 24(4), 109-116.
5. Thompson, L., & Martin, C. (2022). "The Importance of Early Detection of Drilling Hose Wear to Prevent Operational Downtime." Energy Efficiency in Extraction, 36(7), 189-196.
6. Young, T., & Harper, G. (2020). "Comprehensive Guide to Drilling Hose Condition Monitoring and Performance Assessment." Petroleum Engineering and Maintenance, 29(6), 78-85.
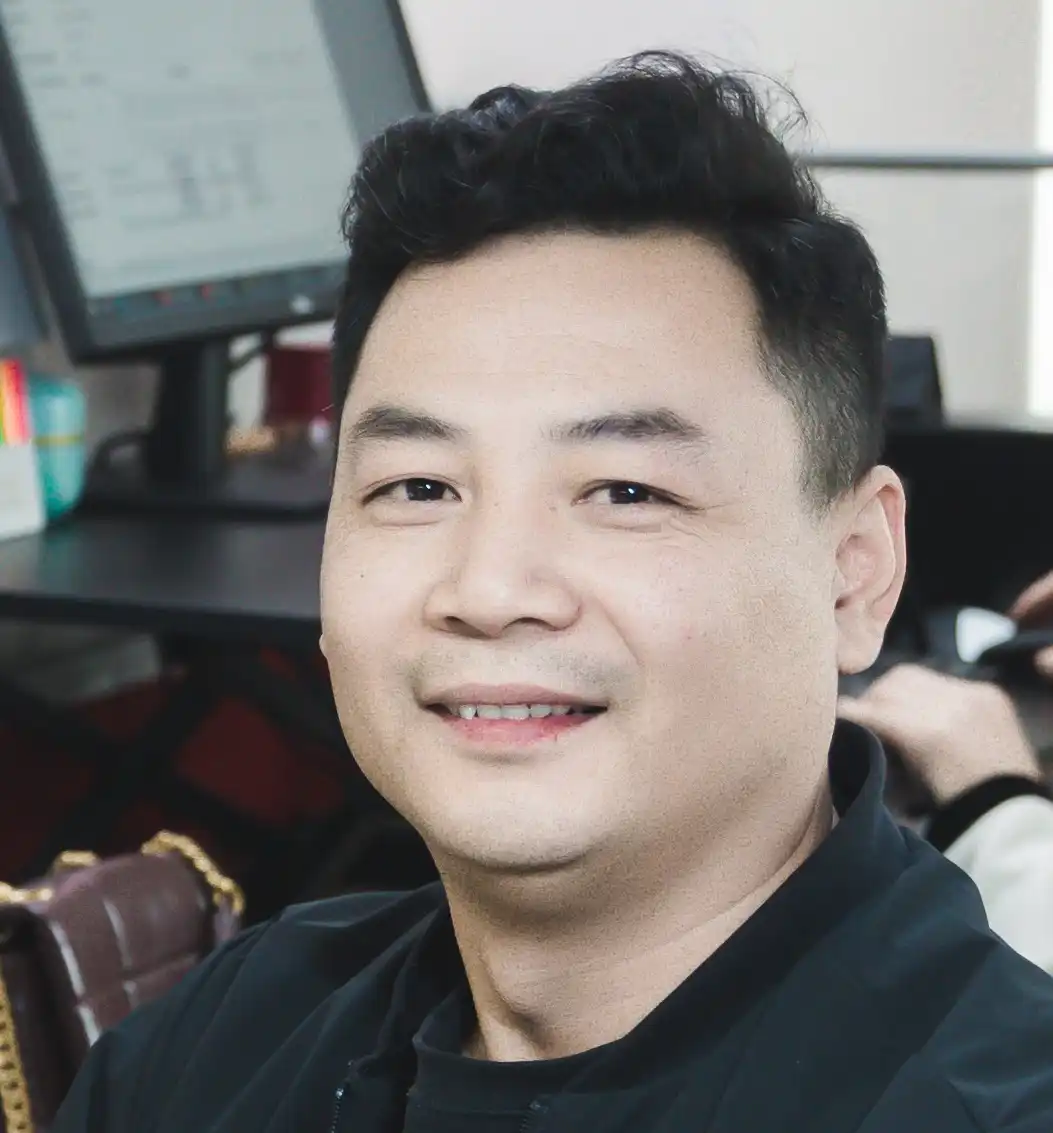
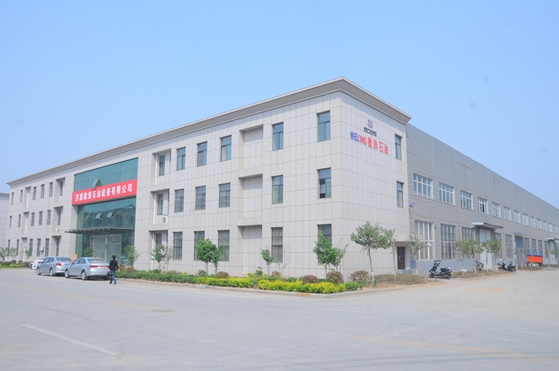
CHINA WELONG - 20+ years manufactuer in oilfield tools